Our operations rely on securing high-quality, cost-effective, and fit-for-use materials and services from suppliers who are expected to adhere to PMI’s environmental, social, and governance (ESG) requirements. In addition to strengthening regulatory compliance and preventing reputational risks, responsible supply chain management enhances our resilience and supports our ability to secure the resources needed to deliver on our company purpose. At the same time, it acts as a lever to make tangible positive contributions to environmental and social issues. We seek to actively engage with our suppliers to minimize our social and ecological footprint, and we strongly believe we can bring positive value to those with whom we collaborate.
Our approach
We aim to purchase goods and services from suppliers at best value, commensurate with business requirements, while appropriately managing supply, financial, legal, quality, and sustainability requirements. We seek continuously to identify and address current and potential risks, while also seizing opportunities to create a positive impact in the communities in which we and our suppliers operate, thereby increasing the sustainability performance of our supply chain. We work with suppliers and contracted tobacco farmers to achieve a solid economic performance and tangible environmental and social improvements.
Our approach to sustainable supply chain management is built on the following core principles:
- Proactive engagement is key to fostering open and transparent relationships with our suppliers in which expertise is shared and built together.
- We take a risk-based approach, deploying tailored tools and interventions and prioritizing areas in which we can have the greatest impact.
- We seek to support our suppliers in continuously improving their sustainability performance and achieving the highest standards of compliance.
- We leverage our reach and understanding of our supply base to implement impactful programs and accelerate progress in our sustainability corridors, such as our efforts to tackle climate change, protect nature, and promote fair working conditions.
Our supply chain sustainability strategy is grounded in our Responsible Sourcing Principles (RSP), which align with the UN Guiding Principles on Business and Human Rights (UNGPs), the Ten Principles of the UN Global Compact, and International Labour Organization (ILO) Conventions. The RSP, together with its corresponding Implementation Guidance, detail our ambitions and set process and performance standards for our suppliers of materials and services, from the direct materials used in manufacturing our products to the goods and services required to run our business.
We expect all our suppliers—and in particular our critical suppliers—to demonstrate high sustainability performance and compliance with the expectations of our RSP and Good Agricultural Practices (GAP). And we have set a commitment to source sustainably from all our critical suppliers by 2025.
Adherence to our RSP—and GAP for our tobacco supply chain—is built into our contractual agreements with suppliers. We monitor the activities of our critical suppliers through a suite of tools, including third-party assessments, on-site audits, and field visits.
We apply tailored due diligence instruments and mechanisms within specific segments of our supply chain. In our tobacco supply chain, our work is governed by GAP and our Agricultural Labor Practices (ALP) Code, which are operationalized at farm level by field technicians working year-round with the farmers contracted by PMI and our suppliers.
Our Procurement organization leverages the work of the Responsible Business Alliance (RBA)—the parent organization of the Responsible Minerals Initiative (RMI)—in our non-tobacco supply chain and of EcoVadis in our direct materials, indirect materials and services, technical procurement, and advanced procurement supply chains.
Our RBA membership and EcoVadis partnership allow us to operationalize and implement due diligence in these complex and dynamic segments of our supply chain.
The sustainable sourcing of goods and services involves a broad cross-functional collaboration within PMI, driven by our Procurement and Leaf teams and overseen by our Senior Vice President, Operations.
Overview of our supply chain in 2021
With over 29,000 tier 1 suppliers across more than 180 markets, our supply chain spend amounted to approximately USD 11.1 billion in 2021.
Our global supply chain is organized into two main streams—direct spend (focused on materials used in the manufacture of our finished products) and indirect spend (focused on goods and services necessary to operate our business)—and seven categories:
Over the years, the management of our supply chain has proven sufficiently robust, flexible, and efficient to support our operations’ evolving needs and PMI’s business transformation. Currently, our global supply chain supports our two main finished product streams, with a continued increase in the proportion of resources allocated to smoke-free products versus combustible cigarettes (smoke-free products accounted for 35 percent of our supply chain spend in 2021, up from 33 percent in 2020).
From a sustainability standpoint, the supply chain categories exposed to the highest risks pertain to our direct spend and include:
- Tobacco production across Africa, Asia, and South America, with the main risks in the areas of working conditions, child labor, climate change, access to water, and the socioeconomic well-being of farming communities
- Electronics manufacturing, with the main risks relating to working conditions
- Paper and pulp-based materials, with the main risks linked to deforestation, biodiversity loss, and climate change
During the year, the supply of direct materials has been under pressure due to high demand for primary commodities, a global transportation shortage, congestion, and cost inflation, mainly driven by energy prices. Thanks to robust business contingency plans and the efforts of our Operations team, we have been able to manage shortages to ensure stable production in our manufacturing centers. We have also expanded our supply base to secure additional supplies and mitigate the impact of inflation. Regrettably, the prolonged impact of the global semiconductor shortage limited our ability to realize the full potential of IQOS development and growth in 2021.
Monitoring the sustainability performance of our critical suppliers
Increasing the visibility of our suppliers’ sustainability performance and implementing risk mitigation and performance improvement measures are priorities. In recent years, we have taken critical steps to achieve and deploy tailored due diligence instruments across our direct materials, electronics, and tobacco supply chains.
Our efforts have translated into significant progress toward our 2025 ambition: During 2021, 83 percent of our critical supplier spend was sourced sustainably. Sustainable sourcing is determined based on a minimum threshold score of 45 out of 100 in EcoVadis (for suppliers of direct materials) or 125 out of 200 in RBA (for electronics suppliers); all tobacco purchased from contracted farmers under the integrated production system is considered to be sustainable.
Critical suppliers are those that manufacture or sell components used in the manufacture of PMI finished products (including direct materials, electronic devices and accessories, and tobacco leaf). In addition to the nature of the component, supplier’s criticality is evaluated considering spend segmentation, as well as supply flexibility, as relevant.
Direct materials supply chain
To strengthen our approach in 2021 further, Procurement successfully transitioned our nonelectronics supplier due diligence program to EcoVadis, the leading global service provider of online ESG supplier assessments. This partnership allows PMI to access a vast number of suppliers’ ESG scorecards commissioned by EcoVadis users (leading global companies across industries).
During the year, 87 suppliers representing 90 percent of our total direct material spend (excluding tobacco and electronics) were assessed. Of them, 82 percent demonstrated a high sustainability performance and compliance with our RSP, 18 percent were below the compliance level and required to complete a corrective action plan before doing a reassessment in 2022, and only one supplier will require an on-site audit to be conducted in 2022. The areas for improvement mainly related to labor and human rights, followed by environment, ethics, and sustainable procurement.
The fact-based and detailed EcoVadis supplier evaluations help drive continuous improvement in the areas highlighted. These assessments are available on the EcoVadis digital platform, which allows seamless sharing among all supplier and customer participants, creating an effective collaboration ecosystem. To address the identified improvement opportunities, we plan to launch supplier corrective action plans in 2022. This will be followed by reassessments and on-site audits for suppliers that have more gaps to bridge.
In 2021, we also leveraged EcoVadis’ broad reach and existing supplier base to assess the sustainability performance of strategic noncritical suppliers in other procurement categories of spend, including indirect materials and services and technical procurement. This allowed us to evaluate suppliers representing 22 percent of our indirect spend.
Electronics supply chain
In January 2021, we reached a major milestone: Joining the RBA, the electronics industry initiative for sustainable supply chains. During our first year of membership, we were able to leverage RBA’s best-in-class methodologies and tools, including members’ audit reports, to enhance significantly the evaluation and performance of our suppliers. To increase their knowledge of best industrial practices and use of RBA tools, we engaged new suppliers in the RBA online training platform.
We also participated in RBA’s Validated Assessment Program (VAP)—the standard for on-site compliance verification and effective, shareable audits. Under the program, independent external auditors reviewed our electronics suppliers’ sustainability performance against our RSP. In all, the RBA digital platform afforded us access to 31 RBA VAP audit reports covering tier 1 and tier 2 suppliers, representing 69 percent of our managed electronics supply chain spend. The initial average VAP audit score of our suppliers was 160 out of 200, compared with an RBA average of 127.
In 2022, we aim to achieve higher spend coverage of the RBA audit program, to monitor PMI-managed suppliers and ensure concrete corrective actions are in place where needed.
Conflict minerals
In certain conflict-affected and high-risk parts of the world, four minerals used in consumer goods—tin, tantalum, tungsten, and gold (3TGs)—are sometimes mined using forced labor and used to finance armed conflict. As a result, they have become known as “conflict minerals.” Companies are expected to demonstrate how they respect human rights and avoid contributing to conflict in their mineral-purchasing decisions and practices.
Our 2021 conflict minerals submission to the U.S. Securities and Exchange Commission, covering the year ended December 31, 2020, showed that the smelters from which our suppliers source 3TGs for our Covered Products (as defined in the submission) were either conformant with the Responsible Minerals Initiative audit program (244 smelters) or were undergoing the assessment process (12 smelters).
Another mineral, cobalt, is also linked to unethical mining practices. It is a critical raw material in the production of the batteries used in our smoke-free products.
While the quantities of cobalt required for our products are minor compared with the total global market size, since 2019 we have deployed a due diligence program based on the RMI approach and tools to identify and address potential human rights risks in the supply chains of our suppliers. In 2021, all our battery suppliers fulfilled specific reporting requirements, including furnishing information on the smelters from which they source cobalt.
Subsequent due diligence deploying additional RMI tools indicated that, as of December 31, 2021, each of the 15 smelters from which PMI battery suppliers source cobalt were on either RMI’s conformant list (11 smelters) or active list (4 smelters).
Tobacco supply chain
PMI defines sustainable tobacco production as the efficient and competitive production of quality tobacco in conditions that limit as much as possible the impact on the natural environment and improve the socioeconomic condition of the people and communities involved in its production.
PMI’s Good Agricultural Practices
In our tobacco supply chain, production adheres to our GAP, which define the principles and measurable standards to be met by all those who grow and supply tobacco to PMI. GAP focuses on four areas: Governance, crop, environment, and people. The latter is governed by a dedicated ALP Code.
GAP is mandatory for all suppliers of tobacco to PMI and is reflected in the supply contracts of PMI and its affiliates. Whether we source tobacco from farmers directly or through third-party suppliers, our GAP standards and related monitoring and remediation system apply at farm level. The absence of a clear commitment to act on issues identified, or a persistent lack of action and improvement, can lead to contractual implications for both farmers and suppliers. PMI also reserves the right to terminate contracts immediately in cases of severe violations impacting people, the crop, or the environment.
Maintaining full traceability and monitoring in our tobacco supply chain
To a large extent, responsible sourcing stems from strong relationships on the ground. PMI’s Integrated Production System (IPS) connects leaf suppliers and farmers beyond the customary boundaries of a commercial relationship and enables direct technical support, agronomic advice, financial loans, and various other services. IPS covered 98 percent of our tobacco purchases in 2021. The excluded purchases took place in Indonesia, where an increase in tobacco demand prompted additional purchases, and in Pakistan, where the Government mandated the purchase of nonallocated surplus volume to absorb unpurchased tobacco left in the market after the buying season was over. IPS is vital in providing traceability and visibility in our supply base; it enables the deployment of our GAP and ALP monitoring and remediation system down to the farm level. At the center of this system are field technicians, employed by PMI or our third-party suppliers, who visit each farm on average five to 10 times during the crop season and monitor how well sustainability requirements are applied and commercial processes are working. They provide agronomic assistance, deliver training to farmers, identify and address labor issues, and ensure the implementation of improvement plans.
In 2021, field technicians allowed us to monitor compliance with GAP on all contracted farms. In a few countries facing stringent pandemic-related restrictions, farm visits were adapted and remote support was offered as needed.
The monitoring of GAP implementation can also be performed by third parties, such as specialized NGOs. During the year, we expanded our collaboration in Brazil with Produzindo Certo, a specialist company helping farmers operate more efficiently and sustainably. After a successful pilot carried out in 2020 with the participation of 123 farmers (read more in our 2020 Integrated Report), we extended the scope of the program in 2021 to cover nearly 2,300 farmers. Specialists from Produzindo Certo provided each farmer with a social and environmental diagnosis of their farm, as well as tailored action plans highlighting opportunities for growth and development. Those farmers who commit to adopting the action plan and implementing its recommendations will be visited annually by Produzindo Certo technicians, who will provide assistance and monitor progress over time. The feedback received so far from the farmers has been very positive. They recognize that following the recommendations of this team of specialists will better prepare them for the future, making their farms more sustainable, productive, and fully compliant with market demands and local legislation. In 2022, the work continues. Philip Morris Brazil has set an ambitious target to expand the program to the neighboring states of Paraná and Santa Catarina, covering 100 percent of the affiliate’s farmer base.
Fostering collaboration with our network of suppliers
We need to engage and influence a large number of suppliers—companies with different strategies, priorities, and cultures—to onboard them on our sustainability journey and jointly commit to and deliver on our ambitions. Such partnerships are crucial to sustainability, innovation, and growth, allowing us to accelerate progress. To strengthen and broaden these partnerships, we seek continuously to improve our collaborations with these suppliers and our knowledge of their operations.
A dedicated section of our corporate website describes our company, goals, and purpose to current and potential suppliers, reinforcing the expectations we have regarding our RSP.
To increase awareness of sustainability in our supply chain, share learnings, and maximize impact, we host virtual events, webcasts, and training sessions with strategic suppliers globally. These events cover both general and specific topics, from supplier onboarding and our due diligence platforms to our carbon footprint reduction targets, science-based targets, and partnering on our Zero Deforestation Manifesto.
In 2021, for the second consecutive year, we organized a Global Supplier Recognition ceremony, during which we honored those suppliers that demonstrated excellent performance and contributed most to PMI’s goals.
For the fifth consecutive year, CDP placed PMI on the CDP Supplier Engagement Leaderboard in recognition of our efforts and progress in engaging our suppliers in tackling climate change.
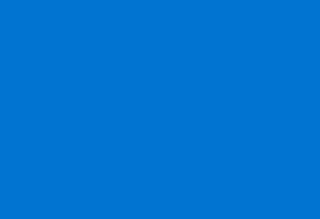
Sustainable supply chain management—topic overview
Read moreThis online content about our Integrated Report should be read in conjunction with PMI’s 2021 Integrated Report. The information and data presented here cover the 2021 calendar year or reflect status at December 31, 2021, worldwide, unless otherwise indicated. Where not specified, data come from PMI estimates. Please also refer to 'This report at a glance' on page 5 of the 2021 Integrated Report for more information. Aspirational targets and goals do not constitute financial projections, and achievement of future results is subject to risks, uncertainties and inaccurate assumptions, as outlined in our forward-looking and cautionary statements on page 252. In the 2021 Integrated Report and in related communications, the terms “materiality,” “material,” and similar terms, when used in the context of economic, environmental, and social topics, are defined in the referenced sustainability standards and are not meant to correspond to the concept of materiality under the U.S. securities laws and/or disclosures required by the U.S. Securities and Exchange Commission.