Integrated Report 2019
INTEGRATED REPORT 2019 |
Progress in 2019
STEP: Supplier due diligence process and platform
The foundation work behind our STEP due diligence platform, launched in 2019, was based on an extensive communication of our RSP to suppliers. Existing and new suppliers will be regularly assessed. Depending on their risk profile and the outcome of the STEP assessment, PMI will engage with suppliers through corrective action plans and regular performance monitoring.
In 2019, we focused STEP deployment on critical suppliers identified by our risk-based criteria. We started to formally onboard suppliers in July. This first wave focused mainly on suppliers of direct materials and electronics. In 2020, our target is to assess the suppliers representing 90 percent of our direct materials and electronics spend through the STEP platform. We are also onboarding key tier 2 suppliers for these two categories. Out of the first wave of assessments, we have experienced a good level of engagement from our suppliers in terms of both response time and completion rate. We attribute this strong uptake to training and communication, webcasts, face-to-face engagement, and strong support from procurement category managers.
Overview of self-assessment questionnaires completed through STEP in 2019
By the end of 2019, the self-assessment questionnaires (SAQs) of the tier 1 and key tier 2 direct materials and electronics suppliers where processed in the STEP platform, with the below results:
The STEP platform is underpinned by an external responsible-sourcing audit protocol provided by Achilles, a leading provider of sustainability supplier evaluation and PMI’s partner in our STEP program. Our platform, based on the principles ISO 19011:2018 and SA8000, is overseen by a steering committee comprising representatives of PMI and Achilles who formally approve the audit process and delivery, including supplier risk profile, governance, audit frequency, and improvement cycle.
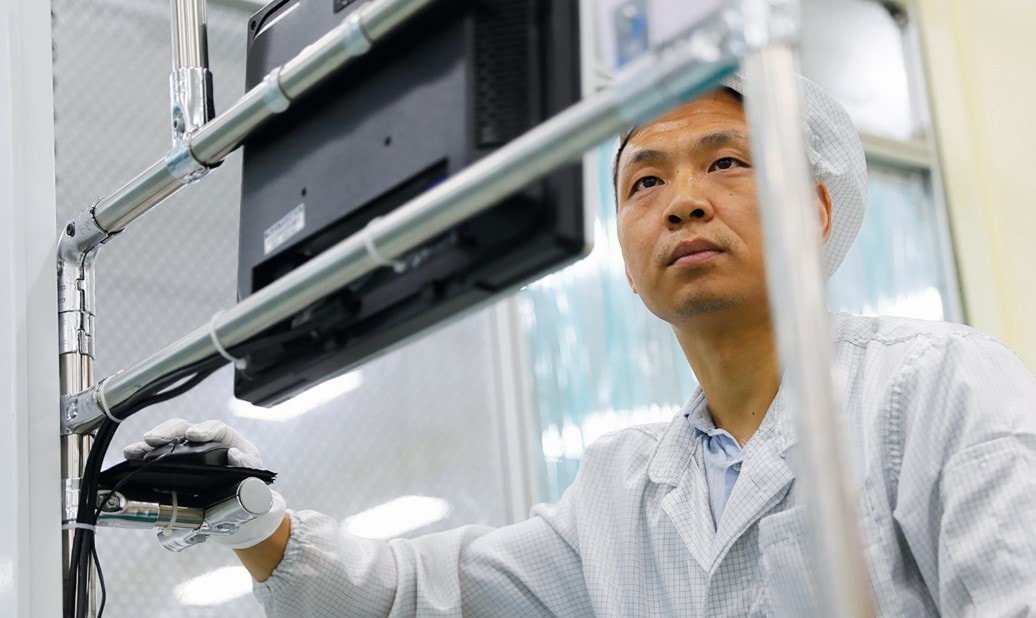
Testing the end-to-end process with a supplier
We tested our end-to-end process by assessing a battery supplier in the electronics category. This supplier completed all steps of the process, from initial risk assessment to the definition of an action plan resulting from an on-site audit conducted on its premises in China. This supplier was classified as medium risk according to the initial risk model screening, which required the completion of the entire set of STEP questionnaires.
The outcome of the online self-assessment highlighted a need for further investigation, and the supplier was asked to complete a desktop audit. This audit revealed potential weaknesses in terms of employee working time, fair and equal treatment of employees, and the impact of minerals sourcing on human rights, as well as resource consumption and waste minimization. It was therefore decided to conduct an on-site audit, which confirmed some of the findings identified during the desktop audit and triggered the development of a corrective action plan to be implemented in the course of 2020.
Focus on our electronics supply chain
Responsible sourcing at PMI goes further than our STEP process, as we look at risks inherent to specific supply chains. For our electronics supply chain, for instance – which is key to our transformation toward a smoke-free future – we looked at risk exposure with an eye to tackling any potential issues involving our new electronic manufacturing supply base in Asia. On top of our STEP program and regular engagement, which incorporates supplier onboarding and the inclusion of sustainability clauses in supplier contracts, we strengthened our monitoring through specific sustainability scorecards and key performance indicators (KPIs) for our key suppliers and also undertook some preliminary evaluation of conflict minerals usage beyond the 3TG. We scaled up our capacity-building efforts through face-to-face and online training, focused on topics such as labor practices in our supply chain, and expanded our CDP supplier work. To ensure our upstream supply chain fulfills PMI’s RSP, we worked closely with one of our tier 1 suppliers to identify the moderate- and high-risk tier 2 suppliers. Our tier 1 supplier then conducted self-assessment questionnaires and on-site audits. We regularly reviewed the process throughout. In all, a total of 37 tier 2 suppliers were audited and reported their improvement plans.
Beyond due diligence
In our engagement and communications with our electronics suppliers, PMI maintains a clear focus on our RSP. Beyond checking systems and monitoring progress, we aim to build capability and enable positive change in the areas of labor rights, human rights, environmental impacts, and business integrity. One way in which we build capability and knowledge among our suppliers is through seminars, the first of which took place in 2019 with 53 participants representing 28 consumer electronics suppliers (tier 1 and tier 2). Participants tackled topics such as how to implement PMI’s RSP, fire safety, supply chain management, ethical recruitment, and the STEP registration process.
Also in 2019, working with the Responsible Labor Initiative and Responsible Business Alliance Foundation, we reviewed management approaches to forced-labor risk, recruitment surveys, labor relations, training for migrants before they leave home, awareness of labor rights, and other third-party support for migrant workers through the Responsible Workplace Program (RWP). We put a spotlight on recruitment practices and human rights, following the lessons from our pilot project. The aim was to transform the recruitment process given the sector’s reliance on migrant labor. A “new workers’ helpline” was installed at our pilot study supplier as part of efforts to improve the grievance mechanism there. The compliance manager at one of our suppliers commented: “The RWP is a good initiative for the improvement of employee–management communication. The training gave a good understanding to workers about their rights and respect for human rights.”
A women’s empowerment program was launched in 2019 with two suppliers in partnership with Inno, a Chinese nongovernmental organization (NGO), supported by external funding. A core focus was to “train the trainer” so that trainees could propagate the messages and practices more widely. The main training topics were communications skills, problem-solving, and stress management. In all, 140 female workers from the two suppliers took part, enhancing their knowledge and skills as part of PMI’s drive to empower women and promote well-being at work. More workers will be recruited into the program in 2020.
Conflict minerals
Companies are expected to demonstrate how they are respecting human rights and avoiding contributing to conflict in their mineral-purchasing decisions and practices. This applies particularly to the potential adverse impacts associated with sourcing tin, tantalum, tungsten, and gold from conflict-affected and high-risk areas of the world. Our 2019 conflict minerals submission to the U.S. Securities and Exchange Commission, covering the year ended December 31, 2018, showed that the smelters from which our suppliers source are either compliant with the Responsible Minerals Initiative audit program (255 smelters) or have gone through the assessment process (four smelters).
Cobalt
Cobalt is a key raw material in the production of batteries used in our smoke-free products. PMI launched in 2019 a due diligence program with the objective to identify and address potential human right risks related to its sourcing. This program currently covers battery suppliers and smelters. We will provide an update on our work in this domain in our next Integrated Report.
Addressing impacts in our electronics supply chain: Progress update
In our last report, we detailed our work with a key electronics supplier in Asia. The progress made one year on is testimony to a robust process of due diligence, strong relationships, and expert support from Verité, a leading NGO in supply chain sustainability. The potential risks to which PMI was exposed from this supplier relationship centered on migrant-worker practices, working conditions, accommodation, and safety, and oversight of external recruiters.
A second audit in 2019 yielded good news. Interviews with workers revealed a favorable response to our supplier as a result of the due diligence process; they now see that they have a voice and that the management is acting on their concerns. Building on its success in improving recruitment standards and communication, our supplier delivered on its commitment to construct new dormitories in 2019. Further, our team in Asia is working to monitor and engage with suppliers and help improve safety, productivity, and labor conditions.
Furthermore, in 2019, electronics suppliers accounting for 80 percent of our procurement spend attended our capability-building program. We piloted KPIs to better understand working hours in our supply chain. We focused on 19 key suppliers and asked them to submit monthly data about weekly working hours and labor composition. This helped us understand the pattern of working hours and to discuss the root causes of excessive hours based on the data. We also integrated working-hour criteria into our scorecard program. Moreover, we introduced a new supplier onboarding process through self-assessment questionnaires, on-site management review, and our STEP program. This illustrates how we work with tier 1 and tier 2 suppliers to constructively resolve gaps in performance and deliver positive social outcomes.
Third-party operators aligning with our standards
In 2019, we visited two third-party operations (TPO) sites that our Indonesian affiliate Sampoerna partners with, and which have a total of 38 facilities in Indonesia. Each typically employs around a thousand skilled people, mainly women, who work predominantly in the hand-rolling of cigarettes. The visits were to determine to what extent the requirements of the RSP could be incorporated into the existing social auditing that was in place. Takeaways from these visits were that working conditions at the third-party sites are very good, showing an environment that goes beyond legal compliance and where the welfare of the workers is treated as of primary importance. In addition, the Industrial and Employee Relations department of Sampoerna conducted a formal annual assessment of working conditions, compliance, pay, benefits, and environment, health, and safety. All 38 sites scored above 92.8 percent in this assessment.
The TPO we visited already have examples of systematic management of social impact, such as capping the number of internships and defining a time period (12 months) for internships. This is important because internships are not subject to Indonesia’s minimum wage laws, and we want to ensure they are not used to circumvent these laws. The TPO are looking to embrace PMI’s RSP more formally in their site-based assessments. This presents an opportunity to bring around 38,000 more workers into the scope of PMI’s human rights standards. We see signals of strong performance – at scale – across TPO from the reviews conducted so far. Next steps include deeper communication on RSP implementation, a governance process to guide the integration, and the development of training modules.
Good Agricultural Practices for tobacco farming
In our agricultural supply chains, sourcing is managed in accordance with our GAP standards and our ALP code (see also here). GAP is a demanding set of standards focused on governance, crop, environment, and labor practices:
-
PMI expects suppliers to have in place the necessary governance, procedures, and processes to manage contracts, field technicians, visits, and training.
-
The crop must meet certain criteria on quality, style, integrity, and regulatory compliance. GAP also demands that the crop is grown with the appropriate seed variety, with the correct plant nutrition, and using effective integrated pest management to minimize the use of crop protection agents while improving the yield.
-
The environmental demands of GAP help farmers to use natural resources efficiently and minimize negative impacts such as deforestation, soil degradation, and pollution.
-
PMI is committed to eliminating child labor and other labor issues on all farms from which we source tobacco. Our ALP code guides our work in this regard.
To a large extent, responsible sourcing succeeds when relationships on the ground are strong. At PMI, our Integrated Production System (IPS) connects leaf suppliers and farmers in a commercial relationship that enables direct technical support, agronomic
advice, financial loans, and various other services. This is especially important when markets are uncertain or when prices become volatile. The support means the farmer can sell his or her production at a fair price.
PMI's tobacco supply chain
At the center of the system are field technicians: Men and women who support the implementation of GAP and monitor how well commercial and contractual processes are working. Some 2,875 field technicians – 170 employed by PMI and 2,705 by our third-party suppliers – implement GAP among the 335,000 farmers from whom we source tobacco. These technicians are facilitators of progress on the ground. They continuously build relationships with the farmers, most of whom cultivate less than two hectares of tobacco in isolated locations with only basic infrastructure. The trust they garner is crucial to the effective monitoring of GAP and ALP. It is often their pragmatic and sensitive interventions that overcome the barriers facing a program of responsible sourcing.
On top of the farm-by-farm monitoring by field technicians, since 2016 we have been assessing the conformity of our contracted tobacco farmers and suppliers to the GAP standards through the industrywide Sustainable Tobacco Program (STP). Managed by independent supply chain management specialist AB Sustain, the program generates performance ratings that allow us to prioritize where corrective actions are required. The STP process includes:
annual self-assessments completed by tobacco suppliers (reviewed by AB Sustain);
on-site audits conducted by AB Sustain among a sample of contracted farmers; and
a comprehensive review of tobacco suppliers’ policies, procedures, and documentation to assess the level of STP/GAP implementation.
In 2019, in order to focus on developing a new STP 2.0 program, the industry did not run collective assessments with AB Sustain. However, PMI continued to assess conformity through annual self-assessments by all our suppliers. Additionally, Control Union conducted assessments for PMI in three locations in 2019.
In 2019, PMI assessed conformity of all our tobacco suppliers with the GAP standards of the industry-wide STP through annual self-assessments
Next steps
We plan further expansion of our STEP program across all the spend categories in our supply chain and all geographic areas. In 2020, we will build on our 2019 desktop and on-site audit pilots, and we are planning to deploy STEP to also cover nonstrategic suppliers, defined by spend thresholds. In parallel, we will look to identify and possibly select additional due diligence digital tools with which to deploy our compliance program to our tail spend. Additionally, we will expand our benchmarking activities to leverage other industry standards and possibly collaborate with individual companies on supply chain due diligence programs.
Building on the progress we have made with our tier 1 suppliers in the electronics supply chain and the initial deployment among tier 2 suppliers, we plan to expand our engagement to all tier 1 suppliers in order to evaluate also our tier 2 suppliers against our RSP. Since relationships and capability-building are key to improving sustainability performance, we will continue organizing and delivering seminars, webcasts, and other capability-building measures. Through 2020, we will be maintaining compliance with GAP and ALP on the ground to allow measurable impacts to show changes in environmental, social, and economic conditions.
This online supplement to our integrated report should be read in conjunction with PMI’s Integrated Report 2019. The information and data presented in this online supplement cover the 2019 calendar year or reflect status at December 31, 2019, worldwide, unless otherwise indicated. Where not specified, data come from PMI estimates. See About this online supplement for more information. Aspirational targets and goals do not constitute financial projections, and achievement of future results is subject to risks, uncertainties and inaccurate assumptions, as outlined in our forward-looking and cautionary statements.