Integrated Report 2019
INTEGRATED REPORT 2019 |
An environment that keeps everyone safe and protects the well-being of all is a prerequisite to productive work. We are committed to providing a safe and secure working environment for all employees, contractors, and visitors. Our responsibility doesn’t stop at the factory gate; we expect our suppliers and tobacco growers to keep their own workers safe, too.
Why it is important to us and our stakeholders
From a societal perspective, ensuring that people stay safe and well every day is of paramount importance. At work and at home, a sense of well-being helps people maintain motivation and perform at their best and lessens demands on social and healthcare systems.
Promoting a safe and healthy working environment is key for PMI, as the well-being of our employees fosters engagement and productivity. A highly dedicated and productive workforce is an enabler of PMI’s business transformation. Implementing strong safety and well-being management is the right thing to do: It creates and protects value, prevents potential reputational issues, and helps us to manage operational costs. Safe and healthy working environments also equip the company to adapt to megatrends, such as technological progress.
At PMI, we see high-quality leadership and management, as well as a culture of shared responsibility – defined by personal involvement, engagement, and observation – as central to resolving such challenges.
Achieving our aims
In our factories, offices, laboratories, retail outlets, and fleet, we aim for a workplace promoting health and safety, and populated by a motivated workforce.
Our aim:
<0.3
Total recordable incident rate for employees and contractors by 2025
Working conditions at PMI are governed by our Guidebook for Success (our code of conduct) and our health, safety, and security principles and practices. Our safety management system enables us to monitor health and safety performance across all our manufacturing facilities. In 2019, we achieved the global multisite certification to ISO 14001 and OHSAS 18001 of 98 percent of our factories producing more than 3 billion cigarettes equivalent annually. At site level, each manufacturing operation has a dedicated team that ensures the standards are delivered on the ground. Team members constructively challenge their peers and benefit from cross-auditing by colleagues at other sites.
We routinely update our systems and train our staff. Our corporate targets on incidents help us evaluate the effectiveness of our safety policies and programs. All incidents in our manufacturing operations are subject to in-depth root cause analysis, and we apply the same thorough approach to all contractors in our manufacturing facilities.
In our manufacturing operations, the primary focus in 2019 was to implement the use of behavioral observation systems (BOS). Within such a culture, everyone involves themselves in openness, care, observation, and behavior reinforcement. We help move this culture change forward through communication with employees and safety alerts or notice boards. Every person’s contribution counts – a fact we recognize through awards and other means of acknowledgment. Through BOS, we are further embedding safety into the DNA of the organization in a planned, structured, and standardized way. It will make a significant contribution to delivering on our safety ambition.
For our fleet of almost 24,000 vehicles, a total of 160 people are allocated to manage security and market safety, led by our global Head of Market and Fleet Safety. These personnel run safety programs, training, and engagement at the country level, using fleet diagnostics and performance indicators to evaluate progress annually. Our specific medium-term target in fleet operations is to reduce high-severity collisions, with an ongoing goal of eliminating fatal accidents completely.
Also important to us is achieving our well-being goals by continuing to focus on a variety of initiatives grouped under our BalancedYou program. Here, we support healthy lifestyles, including by providing medical assistance and promoting physical activity, healthy eating habits, and work-life balance.
Many teams across PMI manage and contribute to health and well-being, including Health & Safety, Inclusion & Diversity, and People & Culture (our human resources team). BalancedYou is “owned” by employees; it is governed at the country level by health, safety, and well-being (H&WB) committees composed of workforce representatives. There are currently 55 such committees to ensure maximum employee representation and coverage.
In our manufacturing operations, we focus on instilling a culture of behavioral and observation-based safety.
Progress in 2019
Safety in manufacturing
In 2019, shared responsibility for safety evolved rapidly across PMI. A sustainable and active attitude of care is leading to an interdependent safety culture, guided by our behavioral and observation-based approach.
Initial evidence suggests that our people are beginning to recognize the importance of behaviors such as engagement and openness, endorsement of safe personal actions, anticipatory feedback, and safety reporting. The challenge is to standardize how we create a BOS culture and then to formulate tools that work.
We share instances of success around PMI. For example, an operator in Argentina shared that he has overcome his initial skepticism of the observation-correction method: “Now that we apply BOS every day, I believe it is a good practice. It makes me more alert, and I feel more conscious of what is unsafe for me.” Many teams try out the BOS approach at a simple level first; for example, asking a colleague not to walk while using a mobile phone. In Portugal, after our teams returned from vacation, we noticed a higher accident rate, so we used BOS in a “Back to Work” project to help people return to the normal heightened state of safety awareness Read more in our case study: A model for integrated sustainability.
To promote an “active caring” approach in 2019, we delivered training on behavioral and observation-based safety to shop floor teams, supervisors, and high-level management in selected affiliates. To complement this, we provided train-the-trainer sessions to environmental, health, and safety (EHS) managers. Following our pilots in Brazil, Poland, and the Philippines, we rolled out the full training package to all affiliates. Among other positive outcomes, supervisors now have BOS role models, helping them to set expectations and demonstrate leadership.
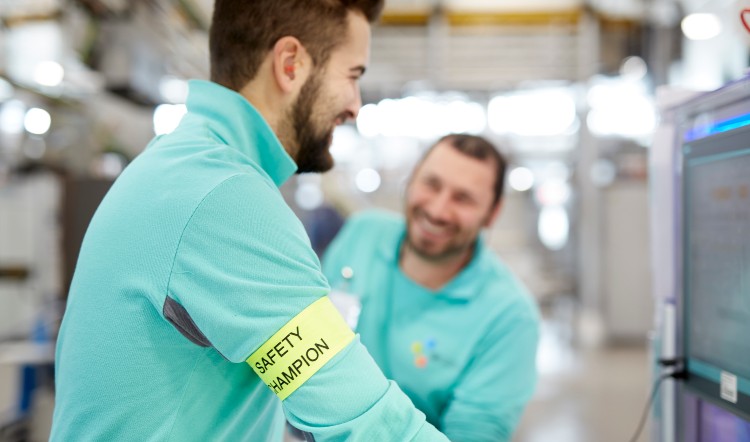
What is a behavioral observation-based safety culture?
It is an approach aimed at focusing employees’ attention on their own and their colleagues’ daily safety behaviors. Drawing on peer-to-peer observations, it allows data-driven decision-making and helps us evaluate and inform our health and safety strategy. BOS encourages every employee to demonstrate his or her personal commitment to safety, to recognize whether a behavior is safe, and to understand the triggers that lead to risky behavior. By creating a culture of mutual observation, we are encouraging colleagues to actively care for one another with kindness and genuine attention. The practice reinforces positive attitudes and behaviors while preventing accidents and injuries.
As an example, a worker may observe a colleague whose behavior poses a risk, perhaps due to fatigue or distraction. In keeping with our employee culture, the observer would address the person involved with respect and calmly offer assistance. More generally, we might use an “active care” training module to inspire colleagues demonstrating unsafe behaviors to analyze the cause of their behavior or condition. We would then offer support and solutions, and seek a personal commitment to safer actions. On an ongoing basis, we review the factors that drive or trigger particular unsafe behaviors (“safety triggers”) to prevent them happening again.
And shop-floor workers are more confident in how to observe colleagues and clearer on using the BOS management and reporting tools. In 2019, we trained over 25 percent of manufacturing employees to practice BOS. In 2020, we aim to train and engage all employees and contractors to practice BOS on a weekly basis at a minimum. BOS digitalization will allow us to better understand the causes of unsafe behaviors and to be more focused in our prevention programs.
In 2019, based on data for PMI employees and contracted employees, our lost time incident rate (LTIR) in manufacturing was 0.06 (2018: 0.07), against a target of 0.10 or less. Our equivalent total recordable incident rate (TRIR) was 0.17 (2018: 0.20), against a target of 0.30. No employee or contractor fatalities occurred in our factories in 2019. The rates are improving versus 2018, thanks to the improved quality of accident root cause analysis and to the BOS deployment initiated in the second half of 2019.
In parallel, 2019 saw extensive work on in-depth root cause analysis for all incidents affecting employees and contractors. This involved analyzing the risk, its controls, impact severity, predictability, and near misses, helping us to direct resources to priority areas.
Allied to the evolving safety culture at PMI is the work we are doing to influence working conditions at third-party operators. In 2019, we visited two third-party manufacturing sites in Indonesia to review labor conditions, and we assessed health, safety, and well-being as part of this. Each third-party site typically employs around a thousand skilled people, mainly women, who work predominantly in the hand-rolling of cigarettes (please see page 87 for more information).
Focus on fleet safety
Driving presents a risk to workers at PMI. We have almost 24,000 cars on the road, covering around 500 million kilometers a year. The safety risks faced by our sales and distribution personnel, especially those at the wheel, are exacerbated in regions where road conditions can be more treacherous. Road traffic accidents not only affect PMI staff but also the public, so fleet safety management is a top priority.
PMI’s fleet safety management system covers driver training, vehicle safety, and driver behavior; our procurement policy ensures maximum safety features in fleet contracts.
Although we continue to reduce collisions, it is to our deep regret that we again endured road traffic fatalities in 2019, including one PMI employee and 10 members of the public. The accidents occurred in six countries in Asia and South America, involving challenging circumstances related to distracted driving and disrespect of basic defensive-driving techniques, such as traffic anticipation and maintaining safe speeds for the road conditions. The lessons learned include an intensified need for proactive risky driving detection, followed by adequate actions and a balance among behavioral programs, technology implementation, and a fleet safety management system.
PMI’s fleet safety management system covers driver training, vehicle safety, and driver behavior.
The challenges we face in delivering safe working conditions relate to road conditions, law enforcement, and driving culture. Drivers almost always work alone, and we recognize that they may at times be under stress, so organizational risk controls can be impaired. Technology can help manage these risks, and we use telematics to monitor driver behavior to improve safety and efficiency. In various countries, the introduction of telematics, coupled with other elements of our fleet safety management system, has significantly decreased our collision rate. For instance, it dropped from 2.88 to 0.91 in Ukraine between 2014 and 2019, from 0.87 to 0.49 in Egypt between 2017 and 2019, and from 5.63 to 2.46 in South Africa between 2018 and 2019. Read more in our case study: Bringing a smoke-free future to the African continent.
We will continue to focus on road safety. In 2019, globally, we reduced collisions per million kilometers driven, achieving 0.87 (2018: 0.91), and we are now working toward our target of <0.80 by 2022.
In 2019, we reduced our fleet collision rate per million kilometers driven, achieving 0.87 (versus 0.91 in 2018)
Employee well-being
The pace of change in the working world creates stress and anxiety, and we recognize that this may be heightened in some instances by PMI’s current transformation. We consider it our duty to equip our employees to better cope with stress and uncertainty.
Fundamental to this are the flexible work arrangements that encourage a healthy work-life balance, currently available across 85 countries where our employees are located. These arrangements include the possibility of remote work, a compressed working week, part-time employment, and unpaid leave.
Our employees want to be great parents and great professionals, and we support this by running pre-maternity, post-maternity, and new-father workshops, as well as by facilitating peer-to-peer support through the employee-run Parents@PMI network piloted in Switzerland. Building on the success of this pilot, we shared a toolkit with all our markets in order to support them in building their own parents networks if relevant. These complement employee benefits such as health insurance, paternity and maternity leave, nutritious canteen food, and sporting facilities.
On top of flexible working arrangements and life-centered benefits, and to further focus on mental health issues, we offer a blend of awareness raising, training, and coaching. To support general employee health and well-being, and to foster a better working environment, we invite employees to conduct their own health risk assessment to monitor their mental and physical biometric health data, and to act on it accordingly.
Other health and well-being initiatives for employees continued in 2019 through our Health & Well-being online platform. In some of our factories, for example, there is on-site blood pressure monitoring by nurses. Also, at shop floor level, we provide advice on healthy lifestyles, including nutrition, heart and back health, exercise, alcohol abuse, heat stress, and dengue fever risk, for instance, depending on site location. Further, we promote active involvement in our H&WB committees as a way to improve employee involvement in how BalancedYou evolves.
Employees’ mental health was also on the agenda of our work with the European Works Council regarding the Stress Management Directive.
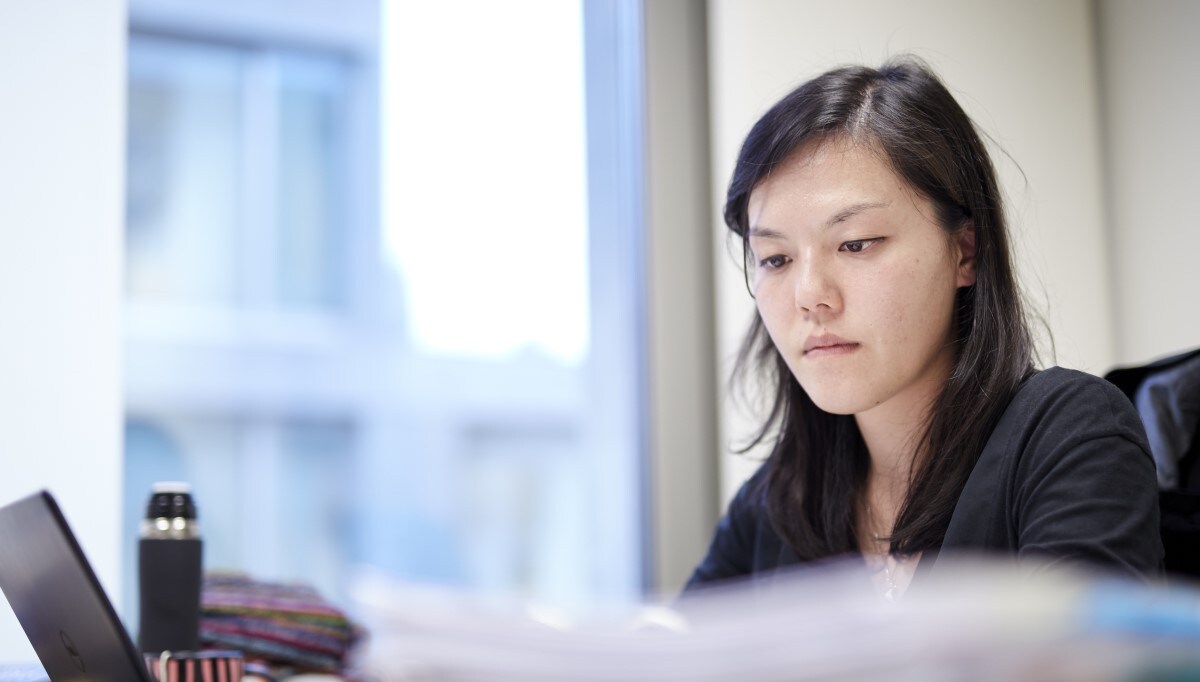
Focusing on mental health in our Swiss operations
In 2019, PMI focused its well-being program in Switzerland on mental health, including stress management and resilience, in line with the WHO’s special initiative for mental health. We undertook various activities throughout the year, including health and well-being weeks dedicated to mental health and resilience, with more than 500 employees participating in workshops. And we tailored some of our training courses to better reflect mental health considerations. For example, our Leadership Fundamentals training now includes a focus on strengthening managerial soft skills. We also ran a pilot health risk assessment at our Operations Center throughout summer 2019 to better understand where to focus support on collective health and resilience. The assessment was optional, completely confidential, and provided by an external company. The first analysis confirmed the continued need to focus our efforts on mental health and resilience; we will use the findings to build our strategy and roadmap with targeted actions to be delivered throughout 2020. These actions will focus on individual needs, leadership behavior, and organizational stress.
A snapshot of our efforts to promote employee well-being, and diversity and inclusion worldwide*
In 2019, we became the first company to receive the global EQUAL-SALARY certification certifying that we pay men and women equally for equal work everywhere PMI operates in the world, covering more than 90 countries.
55 health, safety, and well-being committees are set up at country level, composed of workforce representatives.
Maternity or primary caregiver leave or benefits going beyond local legislation requirements are offered to employees in 77 of our markets.
Women network groups are set up in 22 countries.
Flexible working arrangements are available to PMI employees in 85 countries.
71 countries offer paternity or secondary caregiver leave or benefits going beyond local legislation.
Childcare facilities or contributions are provided in 41 of our markets.
32 markets employ people with disability, and 65 markets have buildings accessible for disabled persons.
We have initiatives or networks to support the LGBTQ+ community in 27 countries.
Next steps
We will continue to deliver initiatives to improve manufacturing and fleet safety, and to meet country-level and global targets, backed up by certified safety management systems within our operations. Specific priorities for fleet safety in 2020 are to refine driver safety, launch new engagement practices in priority markets, and evaluate the potential for a global telematics solution for the whole of PMI. In manufacturing, the focus is to roll out BOS training and push the communication of safety fundamentals. We expect the impact of the BOS safety culture to take effect gradually over the next few years.
Our safety culture shift will continue as new awareness and skills make us all stop, think, and act in anticipation of unsafe behaviors and conditions. The message we will be pushing throughout 2020 is that safety is free of silo-thinking, it is cross-cutting, and it applies at all levels, from shop floor to point of sale and the boardroom. At the top of our well-being agenda in 2020 is improved monitoring and management of mental health and personal resilience. Based on the outcome of our pilot program in our Operations Center in Switzerland, we will refine mental health management tools and programs for employees. We will also report in the future on how our new certification approach is delivering smoke-free PMI offices.
This online supplement to our integrated report should be read in conjunction with PMI’s Integrated Report 2019. The information and data presented in this online supplement cover the 2019 calendar year or reflect status at December 31, 2019, worldwide, unless otherwise indicated. Where not specified, data come from PMI estimates. See About this online supplement for more information. Aspirational targets and goals do not constitute financial projections, and achievement of future results is subject to risks, uncertainties and inaccurate assumptions, as outlined in our forward-looking and cautionary statements.