Integrated Report 2019
INTEGRATED REPORT 2019 |
Our supply chain accounts for a significant part of our social and environmental footprint. With an increasingly integrated and globalized value chain, balancing the security of our supplies with cost efficiency and high quality, environmental, and social standards is a major priority and challenge. Increasingly closer supplier relationships offer opportunities to create sustainable value. At the same time, supply chains may be exposed to potentially significant environmental, social, and governance risks. PMI is fully committed to continuously identifying and addressing such risks, thereby increasing the sustainability performance of our supply chain.
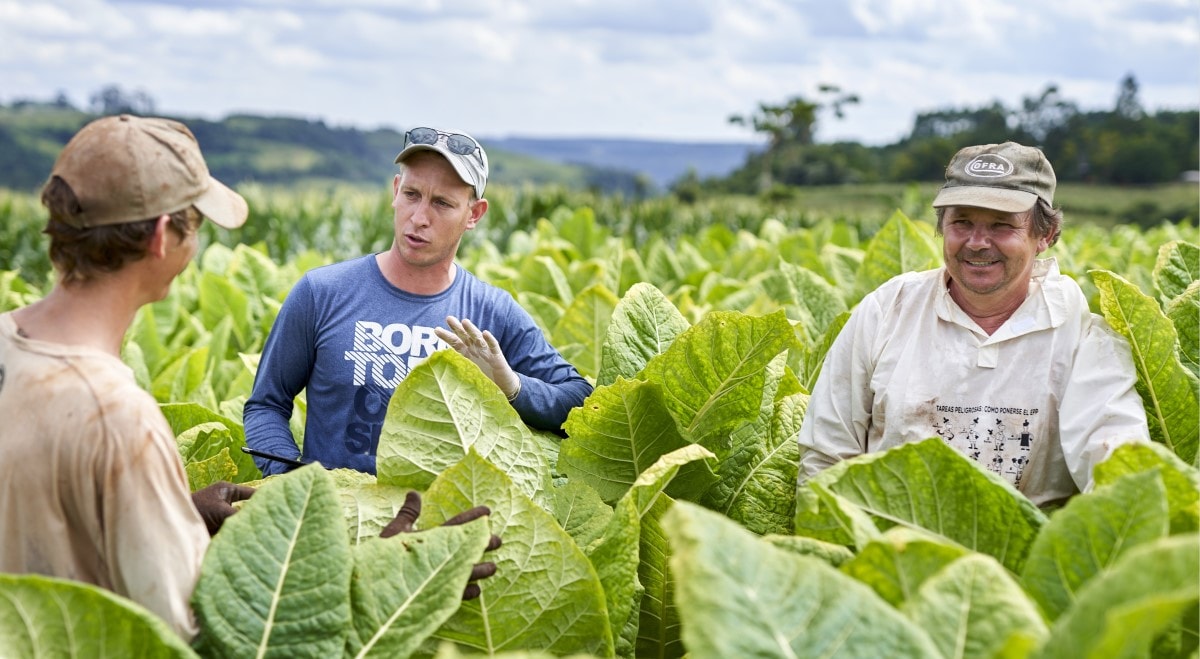
Topic description
To PMI, sustainable supply chain management means embedding sustainability across our procurement strategies and practices, identifying and managing risks and impacts, and continuously evaluating and supporting our suppliers as they work to align their sustainability efforts with our requirements.
Why it is important to us and our stakeholders
Sustainable supply chain management plays a vital role in safeguarding human and labor rights, as well as protecting the health and safety of workers. Optimally, it serves to empower women and alleviate poverty. Moreover, it represents a key lever in mitigating the negative impacts of climate change, reducing greenhouse gas emissions, protecting forests and biodiversity, and promoting energy efficiency, water stewardship, and waste management.
Our business model relies on securing high-quality materials and services from suppliers who are known to us and who adhere to our environmental, social, and governance (ESG) requirements. We recognize that most of our sustainability impacts lie within our supply chain and that it is our duty to manage them responsibly and to be able to secure resources responsibly over the longer term. Responsible supply chain management helps to forge partnerships up the supply chain and improve our knowledge of suppliers. Our risk-based approach means we focus on the most important issues while also supporting efficiency gains, strengthening regulatory compliance, and helping prevent reputational risks.
There are complex connections between managing our sustainability impacts and procuring goods and services. Trying to purchase products and services at the best price while securing appropriate sustainability performance from our suppliers could be perceived as a trade-off. This is not our conception of sustainable supply chain management: We prefer to develop longer-term relationships that enable a sustainable supply chain for both PMI and our suppliers.
Achieving our aims
We aim to achieve measurable, tangible improvements in our supply chain, counting on the commitment and support of our suppliers to continuously improve sustainability performance. Joint efforts offer ample opportunities to strengthen our business relationships and create value for all. PMI aims to purchase goods and services from suppliers at best value, commensurate with business needs, while appropriately managing supply, financial, legal, and sustainability aspects.
Our aim:
100%
Percentage of critical suppliers from whom PMI sources sustainably by 2025
To adhere to the required level of control and minimize the risk of fraud, different teams are responsible for approving commitments, confirming receipt of goods and services, and processing invoices. We expect our suppliers to commit to continuous improvement toward best practices and ongoing compliance. PMI is fully committed to working with and supporting our suppliers on this journey. Mindful of differences across categories and geographies, timelines for full compliance are reasonable and defined. The way we work is grounded in our Responsible Sourcing Principles (RSP), which align with the UN Guiding Principles on Business and Human Rights, the Ten Principles of the UN Global Compact, and the International Labour Organization (ILO) Conventions. The RSP, together with the implementation guidance, set process and performance standards for the suppliers of all materials and services, from the direct materials used in the manufacture of our products to all other goods and services that are required to run our business, including for example, manufacturing equipment, R&D services, and consulting. Sustainability work in our tobacco supply chains is managed at farm level through our Good Agricultural Practices (GAP) and our Agricultural Labor Practices (ALP) programs.
Sustainably sourcing our goods and services goes beyond the work of our procurement team and involves a strong cross-functional collaboration within PMI. With regard to our agricultural supply chain’s impact on climate change, for instance, Procurement, Sustainability Operations, Leaf Department, External Affairs, and R&D work together on addressing the issue. To monitor the adherence of our suppliers to the RSP, GAP, and ALP requirements, we have set up several processes and systems. STEP (Sustainable Transformation Enables Performance) is the supplier due diligence and performance program to achieve supplier compliance with our RSP. It serves as the backbone for sustainably managing our first-tier suppliers; in some cases, second-tier suppliers are also included. In addition to STEP, we also engage with suppliers on more specific sustainability issues, train and empower suppliers, and conduct assessments and audits through third parties as required. STEP is based on the risk management approach that guides our supply chain due diligence framework. Through STEP, our suppliers’ potential ESG risks are determined based on the type of material or service supplied, as well as the country in which the material is produced or the service is delivered.
This inherent risk profile tailors the subsequent evaluation of the suppliers’ performance in addressing the relevant sustainability risks. Suppliers identified as low risk are asked to complete a basic questionnaire, while those characterized as medium or high risk complete a full questionnaire. In addition, high-risk suppliers undergo a desktop audit. Depending on the results of the questionnaire and, as applicable, the desktop audit, the supplier risk profile may be reevaluated and require further due diligence. For instance, a medium-risk supplier that did not achieve the minimum acceptable RSP compliance will be required to undergo a desktop and/or an on-site audit.
Globally, our procurement categories exposed to the highest sustainability risks are electronics manufacturing, wood-based products such as paper and board, and agricultural production across Asia, Africa, and South America. The main risks typically relate to the working and living conditions of migrant workers, deforestation, and climate change. In our tobacco supply chain, the operationalization of our GAP and ALP codes occurs via the 2,875 field technicians who work year-round with the contracted farmers and suppliers of tobacco to PMI. Our ALP program is externally verified by Control Union, specialized in supply chain auditing, and we share their findings and action plans on this website.
Overview of our supply chain spend in 2019
With over 33,200 suppliers across more than 180 markets, our spend amounts to approximately USD 11.4 billion. Thirty-three percent of our total supply chain spend is for direct materials (such as cellulose acetate tow for filters and paperboard for packaging) and smoke-free product devices, 13 percent is on tobacco leaf, and 6 percent on manufacturing equipment. Our large agricultural supply chain ranges from tobacco growers to producers of other agricultural raw materials such as clove, menthol, and guar gum. Our tobacco supply chain includes 16,500 directly contracted tobacco farmers and a further 318,500 growers contracted through 13 third-party suppliers.1 Regardless of whether our tobacco is sourced directly or through third-party suppliers, our GAP requirements and monitoring processes are the same. In 2019, we sourced tobacco from 24 countries, mostly from smallholder tobacco farms of less than two hectares. Our long-term success depends in part on our ability to secure the materials and services required for our operations in a professional and sustainable manner.
In 2019, for the third consecutive year, PMI earned a place on CDP’s Supplier Engagement Leaderboard for our actions and strategies to reduce emissions and lower climate-related risks in our supply chain
The process of our supplier due diligence platform (STEP)
This online supplement to our integrated report should be read in conjunction with PMI’s Integrated Report 2019. The information and data presented in this online supplement cover the 2019 calendar year or reflect status at December 31, 2019, worldwide, unless otherwise indicated. Where not specified, data come from PMI estimates. See About this online supplement for more information. Aspirational targets and goals do not constitute financial projections, and achievement of future results is subject to risks, uncertainties and inaccurate assumptions, as outlined in our forward-looking and cautionary statements.